TechForFuture linkt kunststoftechnologie aan subatomaire fysica
Wetenschappers die de fundamentele structuur van materie onderzoeken zijn gefascineerd door de ongrijpbare neutrino’s. In het internationale KM3NeT-project bouwen ze een ‘neutrinotelescoop’ op de bodem van de Middellandse Zee om de spaarzame lichtsporen van deze deeltjes te kunnen registreren. De gigantische detector bestaat uit 6.000 bollen met elk 31 lichtsensoren. Een zogeheten PMT-support van kunststof houdt deze sensoren in zo’n bol op hun plek; die support is ontwikkeld door onderzoeksinstituut Nikhef. Voor de prototypes gebruikte Nikhef 3D-printen, maar vanwege het formaat en de oplage lopen de kosten en de levertijd van de support onacceptabel hoog op. Het lectoraat Kunststoftechnologie van Windesheim maakte het ontwerp daarom geschikt voor spuitgieten, wat forse besparingen oplevert op kosten en levertijd. Daarvoor moest het de grenzen opzoeken van wat mogelijk is met deze conventionele productietechniek. Onlangs zijn de eerste spuitgietproducten succesvol opgeleverd. TechForFuture legde het contact tussen de wetenschappers van Nikhef en de onderzoekers van het lectoraat Kunststoftechnologie van Windesheim.
Het Nationaal instituut voor subatomaire fysica (Nikhef) doet onderzoek naar de structuur en de onderlinge krachten van de elementaire bouwstenen van ons universum. Om de verbinding tussen fundamenteel en praktijkgericht onderzoek te versterken en innovatie te versnellen, is Nikhef net als collega-instituten de samenwerking met hogescholen gaan zoeken. Dankzij bemiddeling van directeur Alexander Jansen van TechForFuture kwam Nikhef drie jaar geleden in contact met het lectoraat Kunststoftechnologie van hogeschool Windesheim. Het lectoraat richt zich op onderzoek naar duurzaam gebruik van grondstoffen en duurzame productie, met nadruk op recycling, milieu-impact en energiebesparing, en op optimalisering van productontwerp en productieproces. Veel aandacht gaat ook uit naar industriële toepassingen voor additive manufacturing (3D-printen). Achterliggend streven van het lectoraat bij alle onderzoeks- en onderwijsactiviteiten is de maakindustrie in de regio concurrerend te houden.
We hebben interessante handvatten gevonden voor de vertaalslag van 3D-printen naar spuitgieten
Neutrinotelescoop
Concrete aanleiding voor het contact was de ontwikkeling van een neutrinotelescoop in het internationale KM3NeT-project, waar Nikhef aan deelneemt. Neutrino’s zijn subatomaire deeltjes zonder lading en met slechts een minieme massa die nauwelijks wisselwerking ondergaan met andere materie. Daardoor zijn ze ongrijpbaar en dat prikkelt de nieuwsgierigheid van onderzoekers. Om die neutrino’s toch te kunnen detecteren, moeten ze de grenzen van hun meetinstrumenten verleggen. In het donker, diep onder water, willen ze daarom op zoek gaan naar de sporen van het UV-licht dat een neutrino achterlaat als die met de kern van een watermolecuul botst. Omdat dit slechts zelden gebeurt, moet de detector gigantisch groot zijn om toch voldoende opbrengst aan ‘events’ te krijgen.
KM3Net is een kubieke kilometer groot en wordt in de Middellandse Zee aangelegd op een diepte van zo’n drie kilometer. De detector bestaat uit 6.000 glazen bollen (digital optical modules, DOM’s) die aan lijnen in het water hangen. Elke bol bevat 31 sensoren, fotomultipliercellen die invallend UV-licht kunnen detecteren. Tussen deze photo multiplier tubes (PMT’s) en het glas is een optische gel aangebracht die reflectie voorkomt en breking van het licht minimaliseert; dit alles om zoveel mogelijk en zo nauwkeurig mogelijk licht te kunnen invangen. De sensoren worden nauwkeurig op hun plek gehouden met een zogeheten PMT-support.
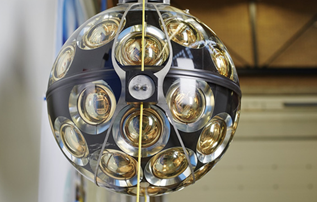
Eén van de 6.000 digital optical modules van de KM3NeT-telescoop
Prototype versus serieproduct
Nikhef is binnen het KM3Net-project belast met de ontwikkeling en productie van de PMT-support. Het instituut maakte zelf een ontwerp en liet prototypes met 3D-printen fabriceren. Technisch bleek deze oplossing zeer geschikt voor prototyping en kleine series, maar voor alle 6.000 DOM’s zouden de kosten en de levertijd zeer hoog uitvallen. Nikhef koos voor 3D-printen omdat deze techniek veel ontwerpvrijheid biedt voor een complex product als de PMT-support. Bovendien zijn er snel, binnen enkele dagen, prototypes mee te maken; voor een conventionele productietechniek moet vaak eerst een matrijs worden gemaakt en dat duurt weken.
Bij grote aantallen ligt het precies andersom. Het 3D-printen van duizenden PMT-supports – forse producten, want de DOM meet 40 centimeter in diameter – zou lang duren en een grote kostenpost vormen. Vijf tot tien machines zouden bij de fabrikant een paar jaar continu staan printen, zo bleek uit berekeningen. Bij conventionele productie vergt het aanlooptraject juist veel tijd en is de matrijs kostbaar. Echter, zodra het productieproces is opgezet, is dat zeer snel, reproduceerbaar en goedkoop. Eén machine zou volstaan om in slechts enkele maanden alle supports op te leveren.
Van 3D naar conventioneel
“Nikhef kwam met een kunststofprobleem dat lag op de snijlijn van meerdere van onze programmalijnen”, vertelt associate lector Geert Heideman op Windesheim. “Denk aan 3D-printen en het optimaliseren van productieprocessen en productontwerpen. Nikhef vroeg ons hun ontwerp van de PMT-support voor 3D-printen te vertalen naar een ontwerp dat geschikt was voor grootschalige conventionele productie.” Maakbaarheid en de vergelijking van productiemethoden op technische en economische aspecten stonden centraal in de opdracht.
Dat lag precies in het straatje van Paul Dijkstra, die als onderzoeker aan het lectoraat is verbonden. Tijdens zijn studie deed hij al veel ervaring op met 3D-printen en conventionele technieken zoals spuitgieten. Heideman: “Ons lectoraat wil bedrijven bekend maken met de mogelijkheden van 3D-printen, als innovatieve en aanvullende techniek en soms ter vervanging van spuitgieten. Dat is interessant voor de machinebouw, waar de series vaak klein zijn. Wij helpen bedrijven dan bij het herontwerp van hun spuitgietproducten voor 3D-printen. Bij Nikhef was het precies omgekeerd. Zij hadden een ontwerp voor 3D-printen en vroegen ons om een herontwerp voor een conventionele productietechniek.”
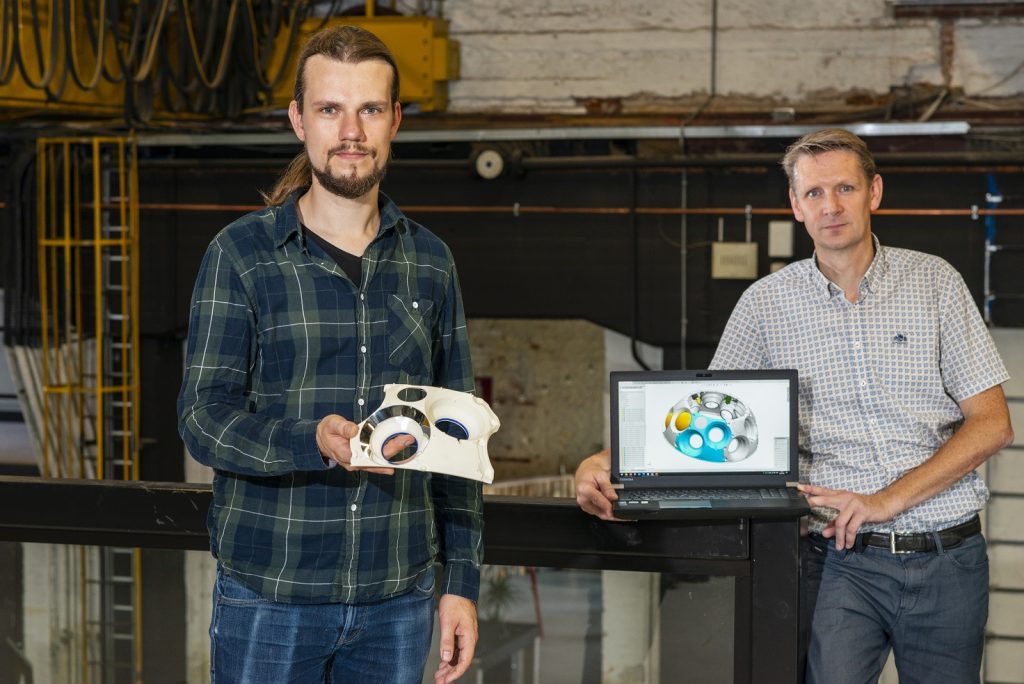
Onderzoekers Paul Dijkstra (l) en Geert Heideman (r) van lectoraat Kunststoftechnologie
Miljoenen besparen
Nikhef had eerst spuitgietbedrijven benaderd voor een herontwerp. Die durfden het echter niet aan omdat zij inschatten dat het 3D-printontwerp niet was te vertalen was naar een spuitgietbaar ontwerp. “Dat was het moment dat Nikhef via Alexander Jansen bij ons kwam”, zegt Heideman. “Paul heeft er met collega’s naar gekeken en concludeerde dat het op het randje zou zijn, maar wel mogelijk. Voor de kunststofwereld was dit echt een uitdaging, die ook een interessante case voor ons onderwijs zou kunnen worden.” Dijkstra: “Spuitgieters kijken vooral naar de kosten, maar in dit geval mocht het product voor spuitgietbegrippen wel duur zijn. Dan nog zou Nikhef bij 6.000 stuks miljoenen euro’s besparen vergeleken met 3D-printen.” Hij onderzocht, ook met inzet van studenten, diverse conventionele alternatieven, zoals spuitgieten, thermovormen en rotatiegieten.
“Spuitgieten sprong er toch wel uit”, vervolgt Dijkstra, “onder meer vanwege het specifieke ontwerp van Nikhef. Dat bestond uit twee halve bollen, die niet identiek zijn omdat de ene halve bol nog ruimte voor koeling van de elektronica bevat. Beide helften waren niet geschikt voor spuitgieten omdat ze extreem moeilijk konden lossen uit de matrijs. We hebben de twee ontwerpen daarom elk opgedeeld in zes identieke onderdelen die samen met nog enkele eenvoudige onderdeeltjes die halve bol vormen. Dat resulteerde in een matrijs die wel goed maakbaar was.” Zo zitten er meerdere ‘slimmigheidjes’ in het ontwerp, aldus Heideman. “Zoals dat opdelen van het ontwerp in kleinere, eenvoudigere delen. Dat lijkt voor de hand te liggen, maar je moet er wel opkomen. Nog altijd is het een complex product, met gekromde vlakken, schuiven, scheenpennen en bewegende delen, maar het lossen uit de matrijs is nu wel mogelijk.”
Kwaliteit boven alles
Over dat herontwerp ging de nodige tijd heen, verklaart Dijkstra. “Het heeft even geduurd voor we echt alle eisen in beeld hadden die aan het product werden gesteld. Het was zo gemakkelijk om een ogenschijnlijk klein dingetje over het hoofd te zien dat wel ten koste van de nauwkeurigheid zou kunnen gaan.” De materiaalselectie vroeg ook de nodige aandacht. “De keuze viel op ABS, een commodity plastic dat niet te duur is, goed spuitgietbaar is en weinig krimp vertoont. Een uitdaging vormde de chemische compatibiliteit. De gel tussen het glas en de sensor wordt bij assemblage gegoten en moet uitharden, maar dat lukt niet in contact met bepaalde chemische stoffen of verontreinigingen. Het was onacceptabel dat de gel niet zou kunnen uitharden door de aanwezigheid van dergelijke stoffen in het kunststof. Daar hebben we uitgebreid op getest.”
Kwaliteit gaat boven alles bij Nikhef, vult Heideman aan. “Er mogen geen belletjes in die gel komen te zitten, dus moet alles heel schoon zijn. En afdichtingen moeten vloeistofdicht zijn, om te voorkomen dat de hele binnenkant van de bol met gel volloopt. De maatvoering van het product is ook bijzonder, er mag geen enkele verstoring van de precisie in optreden. Er zitten bijvoorbeeld kleine haakjes aan, die de reflectoren (voor een grotere lichtopbrengst, red.) rond de sensoren moeten vasthouden. Die haakjes meten 2 millimeter en de reflectoren zijn slechts een halve millimeter dik. De hoek waaronder zij zijn bevestigd moet precies kloppen. Dat betekent dat je kleine, scherp gedefinieerde features moet kunnen spuitgieten.”
Totaaloplossing
Heideman: “Met inzet van al onze kennis heeft Paul heel veel tijd gestoken in het herontwerp en de simulaties voor spuitgieten. Toen volgde de zoektocht naar een spuitgieter die het wilde produceren. Nog steeds waren er bij spuitgieters veel bedenkingen in verband met de complexiteit. Toch is het ons samen met Nikhef gelukt een aantal partijen te vinden met interesse en de juiste apparatuur en competenties.” Een belangrijk criterium was de assemblage van de onderdelen tot halve bollen. Dijkstra: “Zorgen dat er foutvrij gewerkt zou worden, daar hebben we de spuitgieters op getoetst. De oplossing is dat Nikhef van de spuitgieter compleet geassembleerde PMT-supports ontvangt, inclusief afdichtingen. Het vinden van een aanbieder van een dergelijke totaaloplossing was zeker niet eenvoudig.”
Uiteindelijk koos Nikhef voor Alligator Plastics. Inmiddels is van de ene helft van de PMT-support de matrijs opgeleverd en zijn de eerste proefproducten succesvol gemaakt met spuitgieten. Voor de andere helft is dit traject ook nagenoeg afgerond. Daarna kan de serieproductie beginnen en zal de assemblage van de DOM’s vervolgens bij Nikhef en collega-onderzoeksinstituten in het buitenland plaatsvinden. Voor de Windesheim-onderzoekers is het project daarmee afgerond. Ze zijn “meer dan een beetje trots” dat hun herontwerp is geslaagd. Dijkstra: “Op de eerste gespuitgiete producten had Nikhef na inspectie, assemblage en het opmeten van de maten slechts een paar kleine aanmerkingen. Daarop is de matrijs inmiddels aangepast. Zo hebben we het herontwerp in fasen uitgevoerd, zodat we telkens met minimale investeringen konden toetsen of het werkte.” Heideman: “Die testen waren best spannend en we waren blij dat de eerste resultaten positief uitvielen. Wij zijn nu klaar, maar volgen het project natuurlijk nog met interesse. We blijven zo een beetje betrokken en waar nodig brengen wij nog graag onze kennis in.”
Opstapje naar spuitgieten
Spuitgieter Alligator Plastics zit in Son, bij Eindhoven en dus buiten de Windesheim-regio, en schakelde voor de matrijzenbouw een van zijn vaste partners in. Toch spreken de Zwolse onderzoekers van een geslaagd project. Heideman: “Het levert Nikhef een mooie kostenbesparing op en zij hebben door met ons mee te kijken veel geleerd over kunststoftechnologie. Voor ons was het ook een mooi project, op het randje van wat er technisch mogelijk was. Men begint wel vaker met 3D-printen om later het ontwerp over te zetten, maar dan is spuitgieten altijd het einddoel en is het 3D-printontwerp daarop al afgestemd. In dit geval moest een ontwerp dat totaal niet lossend was, geschikt worden gemaakt voor spuitgieten. Dat heeft ons flink op scherp gezet.” Dijkstra: “We hebben interessante handvatten gevonden voor de vertaalslag van 3D-printen naar spuitgieten.” Heideman: “Die maken het gemakkelijker om 3D-printen te gebruiken als opstapje naar spuitgieten. In dit project hebben wij aan de benodigde basiskennis en ontwerpregels gewerkt. Dat is ook interessant voor bedrijven in onze regio en het versterkt ons curriculum.”